Company | Metallityöliike Tom Nyberg Ky/Anders Nyberg |
Year of construction | 2013 |
Contractor | Best-Hall Oy |
Surface area | about 1,500 m2 |
Volume | 8,380 m3 |
HVAC design | Ab Ingenjörsbyrå Jörgen Holm Insinööritoimisto Oy / Jörgen Holm |
Heating and ventilation solution |
4 pcs Pallas HP Aqua KI with dehumidification function and 1 pc Pegasos HP Aqua with dehumidification function |
Additional heating | district heating |
Contractor | Ilmastointikulma Oy |
Plumbing contractor | LVI-Center Auhtola Oy |
Electricity/Automation | EK-Automatic |
Required heating power | 53 kW |
Ventilation cooling power | 27 kW |
Design air flow (cooling) | 2,790 l/s |
Ideal indoor environmental conditions for a production facility
The ventilation, heating and cooling of the different spaces are handled in a cost-effective and convenient way with dedicated units.
Metallityöliike Tom Nyberg Ky, a mechanical engineering company based in Porvoo, invested in a modern production building at the right time, in the middle of a recession. The coffee roastery of Robert Paulig Oy operated as a tenant in the company’s old hall and needed more space.
– They wanted to include our machine shop for their use. A recession period means lower demand in the engineering industry, so there was time to act as a developer. When the growth starts, there will also be a lack of space also here in Porvoo, Anders Nyberg says.
Flexible possibilities
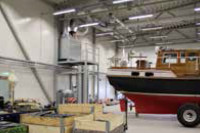
When a company is looking for production and office facilities, location, good indoor conditions and modifiability are key considerations. The operational environment is changing rapidly and the premises must be able to meet the changing needs as easily as possible. In addition to structural solutions that enable division and extension of premises, modifiability must also be taken into account in the building services engineering systems.
Just this kind of modern, modifiable production building was developed by Metallityöliike Tom Nyberg Ky in Tolkkinen in 2013. The company moved its production operations to the new building in early 2014. Now the company can rent out a large hall, either as one entity or conveniently split into two separate spaces, and a modern, lightfilled office space over two stories.
Founded in 1964 and managed by Anders Nyberg, Metallityöliike Tom Nyberg Ky is a family-owned company now in its second generation. Being typical lifestyle entrepreneurs, his parents are not yet fully retired. And the environment to continue could not be better: everything in the new machine shop is designed to work perfectly and the conditions are excellent.
The company’s plot and its production buildings are located right by the Gulf of Finland in Tolkkinen, Porvoo. The view of the sea from the office windows at the shore side of the new production building is something that would cost an arm and a leg in a residential building.
Metallityöliike Tom Nyberg Ky acquired the industrial building, built in 1971, with the plot ten years ago. The building is connected to a district heating network. District heating was one of the options considered for the new production building.
– It would have been the least expensive option in terms of the investment costs, but its operating costs were somewhat unpredictable, Nyberg points out.
A ground-source heating system was also considered, but drilling the energy wells is a quite expensive and – in a high-radon area – a risky solution. The collector pipes could have also been laid on the sea bed, but Nyberg thought that this was not a safe option due to busy ship traffic.
Cooling is an important feature
Nyberg wanted a functional, demand-controlled ventilation solution that would enable both indoor air cooling and dehumidification.
– Today, air-source heat pumps are also used for heating modern, energy-efficient production buildings. They provide heat in the heating season and, if necessary, cool the indoor air in summer. But because work performed in the machine shop also generates a lot of waste heat in winter, we needed a more versatile solution than just air-source heat pumps, Nyberg explains.
In spring 2014, cooling was required when the outdoor temperature has been as low as +8 °C.
The solution designed by HVAC designer Jörgen Holm provides all spaces with optimal conditions in the most flexible, energy-efficient and cost-effective way possible. The production facilities can be divided into three sections. Each section should have a dedicated ventilation, heating and cooling system, because the needs can vary a lot depending on the nature of the operations. The needs in the office and social facilities with an area of about 250 m2 are also different. A different heat distribution system is also used. In the production facilities, air heating is used as the heat distribution system, whereas a water-based underfloor heating is used in the office and social facilities for comfort. The social facilities also have a shower room for staff. The demand for domestic hot water in the production facilities is low.
Professional design
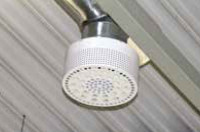
ceiling delivers high-quality supply air
evenly.
The ventilation, heating and cooling solution of the building consists of one Enervent Pegasos HP Aqua unit and four Enervent Pallas HP Aqua KI units – all of these units are equipped with dehumidification function.
– They are an excellent choice because they contain everything needed in one package, Nyberg remarks.
The ventilation, heating and cooling solution of the building is implemented in sections. The heat recovered from each section is transferred via the EnergyBUS to an energy bank, a 5,000-liter Akvaterm accumulator tank located in the mechanical room. From the accumulator, heat is utilized according to need: for the underfloor heating system and domestic hot water system in the office floor, for heating the supply air with the heating coils in the ventilation units, and for reheating the supply air that is dehumidified by cooling on hot summer days.
Electric heating elements are used to provide additional heat at the very lowest temperatures in winter. District heating is also available as a backup system for extremely long cold spells.
The system has already proved to be very energy-efficient over a period of six months: the amount of heating energy consumed for the new hall is only one-sixth (6,500 kWh) of the amount of energy required for heating the old hall.
Designing an air heating and cooling system for a production facility requires both expertise and experience of the designer.
– Excellent indoor climate conditions and good indoor air quality can be ensured by dimensioning the system so that sufficient cooling and heating power is ensured. The air flow rates must be dimensioned higher for air cooling. Sufficient capacity cannot be ensured at the minimum level specified in the National Building Code of Finland, emphasizes HVAC designer Jörgen Holm.